開催日:2019年9月17日
レポート
セミナー
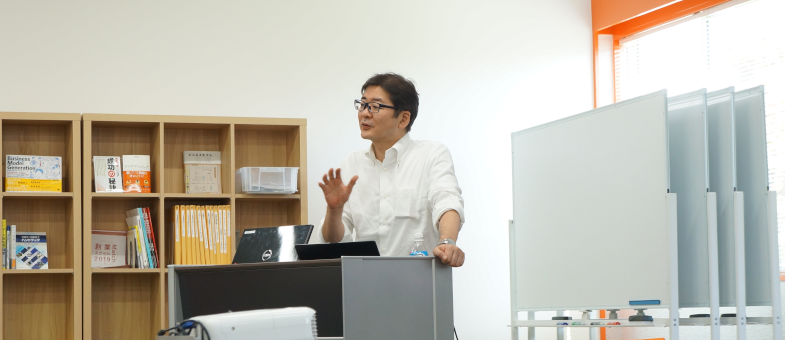
今回レポ―トするイベントは9月17日に開催した、第3回デジタル技術を活用したビジネスイノベーションセミナーです。
テーマは
「生産現場のデジタル化~スマートファクトリー~」。
近年、ロボティクス・IoT・AI等のデジタル技術が進化し、Industry4.0やスマートファクトリーといった概念が世の中に浸透しつつあります。そうは言うものの実際の生産現場では、「何から始めたらいいか分からない」「何が出来るのか分からない」
「そもそもスマートファクトリーの必要性が分からない」といったように分からないことだらけで、なかなかデジタル化に踏み出せていないのが実情ではないでしょうか。
今回はスマートファクトリーを推進するにあたり様々なコンサルや導入実績を有するSIer協会幹事(FA・ロボットシステムインテグレータ協会)兼 ミツイワ株式会社スマートファクトリー推進部 部長 泉貴史氏をお招きし、今後の生産現場のデジタル化による変革とそれを検討する際の指針となるべき知見をご紹介頂きました!
スマートファクトリーとは何か
言葉はよく耳にしますが、そもそも 「スマートファクトリー」 とはなんでしょうか。 私は 「スマートファクトリー=生産現場のデジタル化」 と捉えています。 しかし実際には、生産現場にIoT(Internet of Things)を導入することが主目的になってしまっているケースが非常に多く見受けられます。これは問題です。本来であれば、デジタル技術を導入する前にまず自社の収益・業務プロセス・顧客ニーズを可視化し、方向性を定めることが重要です。 IoTはあくまで手段。IoTに必要な前提条件と、IoTに必要なテクノロジー。それら全てを理解し、全体をオーガナイズする(要件定義する)ことが必要です。
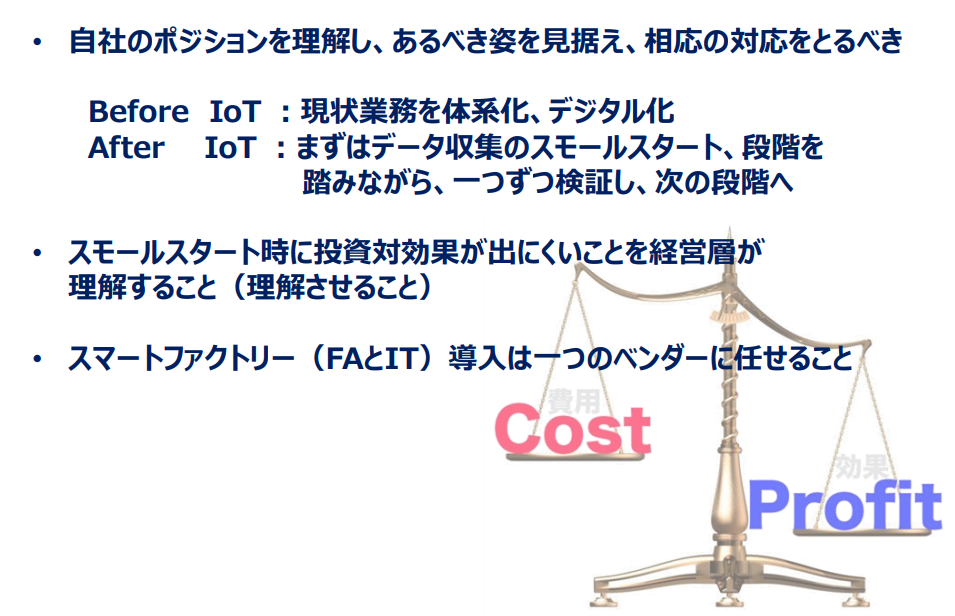
画像選択で拡大表示
問題は、"プレイヤー不在"
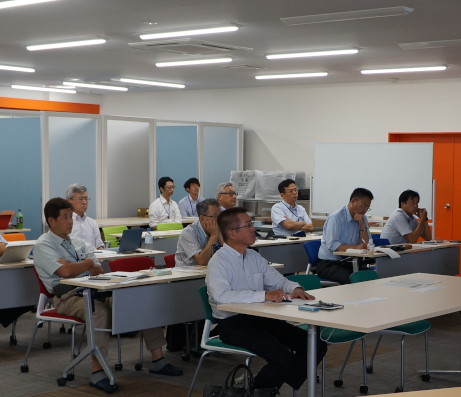
このとき難しいのが、 "プレイヤー不在" です。実際、全てを理解し、生産現場とIT(情報システム部門)をつなげて、オーガナイズできる人は、なかなかいません。IT(情報システム)、FA(工場自動化)、FA-IT連携、制御、生産設備、といった知識を組み合わせて、システム構想を練るのは至難の業です。「生産設備の知識」に長けてる人はいると思います(通常のFA、ロボットメーカー)。 「ITの知識」に詳しい人もいるでしょう(通常の情報システム会社)。 でも、両方の知識を有している人が少ないため、全体最適できずに失敗してしまうケースが多いのです。
解決には、ユーザーとインテグレータをつなぐ人が必要
これは、私たち(ミツイワ)のビジネスコンセプトです。
スマートファクトリーを実現するには、前述したプレイヤー不在や、仕様をまとめられず開発を始めたことによる手戻り、システムの不整合といった様々な課題が存在します。それらを解決し、最適なシステムを導入するためには、ユーザーとインテグレータの間に立ち、双方をつなげる役割が必要です。私たち(ミツイワ)は、そういった役割を担うことで、スマートファクトリーの実現に貢献しようと考えています。
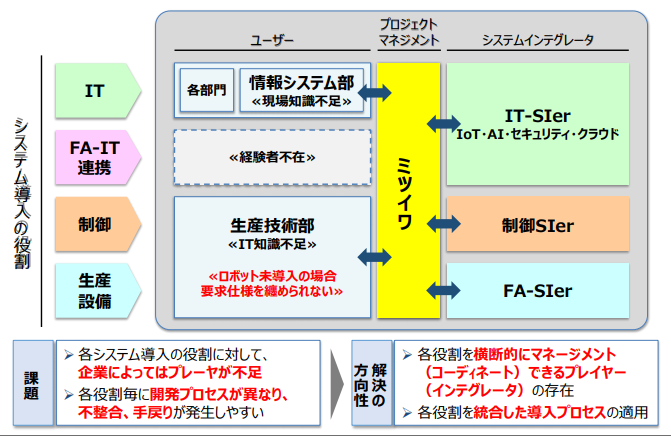
画像選択で拡大表示
スマートファクトリー推進の重要なポイント
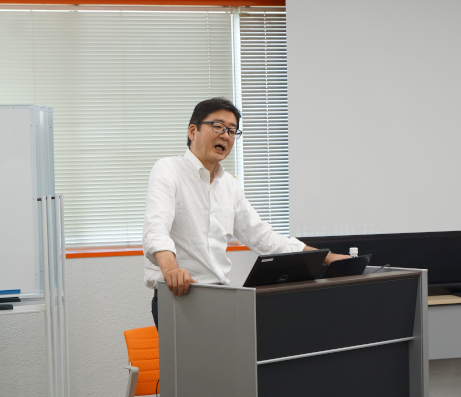
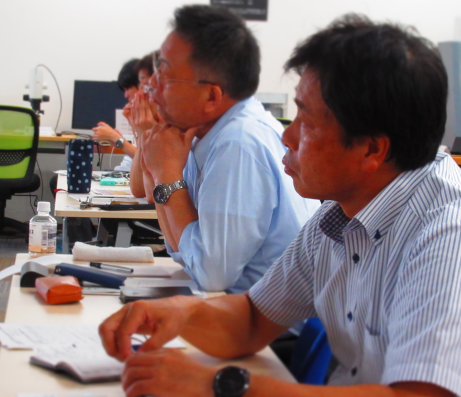
ここまでの話をまとめてみましょう。
スマートファクトリーを推進するために重要なポイントは、以下と考えます。
- 自社のポジションを理解し、あるべき姿を見据え、相応の対応をとること
- Before IoTフェーズでは現状業務の体系化、デジタル化を行うこと
- After IoTフェーズではまずデータ収集をスモールスタート。段階を踏みながら1つずつ検証し、次の段階へ進むこと
- スモールスタート時に投資対効果が出にくいことを経営層が理解すること(理解させること)
- FAとIT導入は両知識を有する「1つ」のベンダーに任せること
導入事例
データ収集はスモールスタートで始める
モデル工場にICTを取り入れ、PDCAを回しながら他工場へ拡大・展開した例です。
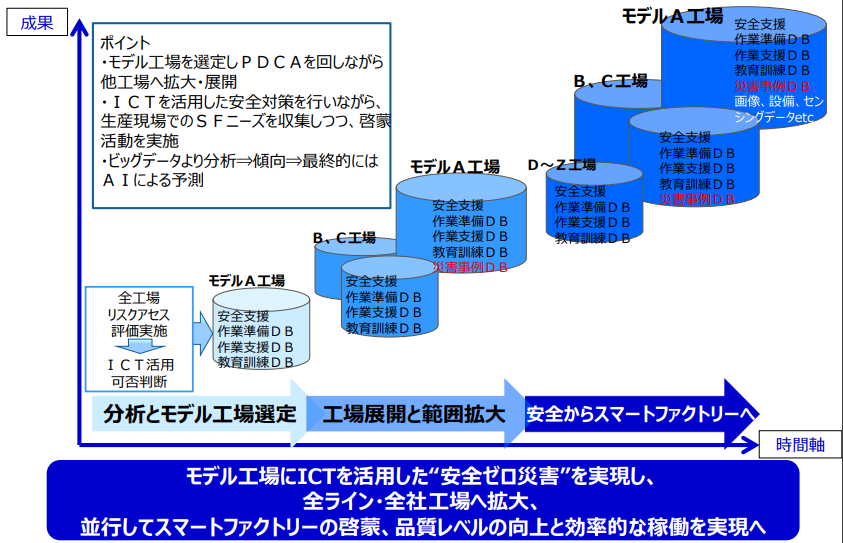
目に見える改善を取り入れる
生産現場のデータを収集し、分析や見える化が可能になると、生産性向上や設置機器の削減などの改善につながります。
そのためにはいかに手間をかけずにデータを収集・分析・見える化・改善まで行えるかがカギとなります。
その1つの手法としてスマートロガーという製品があります。
あらかじめ工場内の作業場所やエリアに複数のビーコンを設置します。そして現場作業者がスマートウォッチを付け、
作業の開始や終了時、またはエリア移動時にビーコンにタッチすることで、誰が・いつ・どこで・何の作業を・どれだけ時間が
かかったか、というデータを簡単に収集・分析できます。
実際にある会社ではこのスマートロガーを導入したことで、生産性2倍やフォークリフト台数半減の改善につながりました。
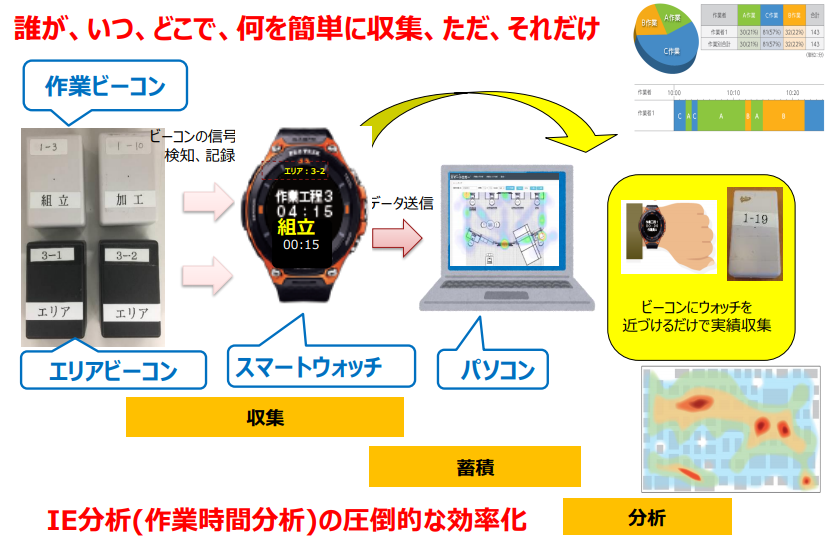
画像選択で拡大表示
高度なスマートファクトリー~リアルタイムの予実(カンバン)~
生産現場にロボットシステムを導入する事で、さらに高度な生産を実現することができます。 例えば部材投入から充填、AI画像判定によるNG品の排出、正式品の包装まで自動化するロボットシステムであればリアルタイムの予実(カンバン)を行うことも可能です。 ロボット・AI・IoT・クラウドといった技術を掛け合わせれば、製造・検査・搬出準備までを自動化することも可能となります。

画像選択で拡大表示
トランスフォーメーションの時代
少し前になりますが、経産省主催のシンポジウムで世耕大臣(当時)がおっしゃっていた言葉があります(2017年 Connected Industriesシンポジウム)。「現場には、日本のモノづくりを活かす為の素晴らしいデータがある。使われていないデータをどう活かすかがカギ。工場、企業、サプライヤーが競争ではなく、協調して密接に繋がることが重要。」
それを受けたパネルディスカッションでは、こんな言葉も出ていました。「今まで競争領域と思っていた(勘違いしていた)領域を、とことん協調領域に仕分け、共創領域を絞り込むことが重要。Connected Industriesは、中小企業(日本の企業の99%)やベンチャーにチャンスをもたらす。」
まさに、そうだと考えています。
これからは、データとデジタル技術を活用して、業務そのものや、組織、プロセス、企業風土を変化させていく。それと同時に製品やサービス、ビジネスモデルも変革させていき、そうすることで競争上の優位性を確立していく。それがデジタル・トランスフォーメーション時代です。
御社のデータ活用状態が、どのレベルにあるか、考えてみてください。
その上で、どう行動を変えていくべきか検討することが、肝要と考えます。
アナログな状態であれば、まず 「デジタルデータにトランスフォームする」。紙の資料をコンピュータが扱える状態に変える、あるいは人やモノにセンサーをつけて情報を収集します。
すでにデータベース等にデータを蓄め始めているのであれば、「デジタルデータをトランスフォームする」。そのデータが何を現わしているのか、分析し、意味を見出すことです。
そこまできたら、「デジタルモデルでトランスフォームする」。現実世界でやりたいことをモデル化してコンピュータに反映させます。リアルタイムの自動制御です。
一足飛びにデジタル化を進めることはできません。一歩一歩、段階を踏んでデジタル化を進めていくことが大切です。
そうしないかった場合の例として、政府がこんなシナリオを発表しています。
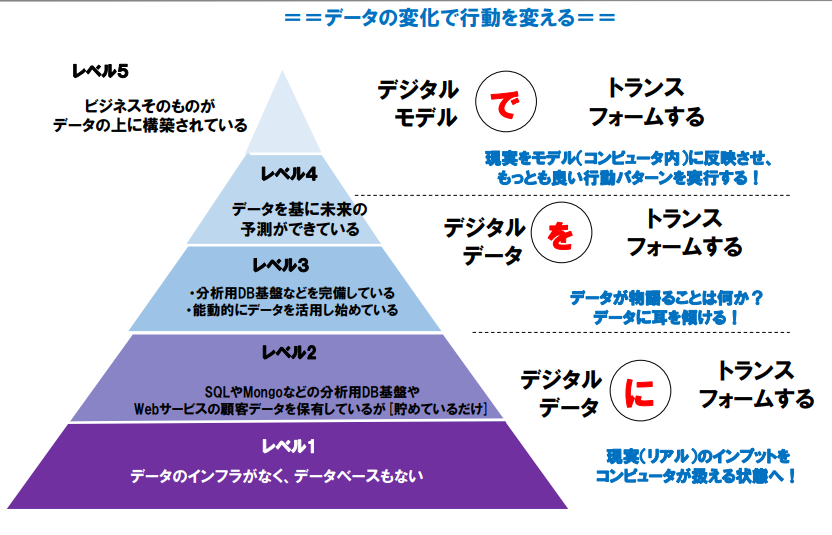
画像選択で拡大表示
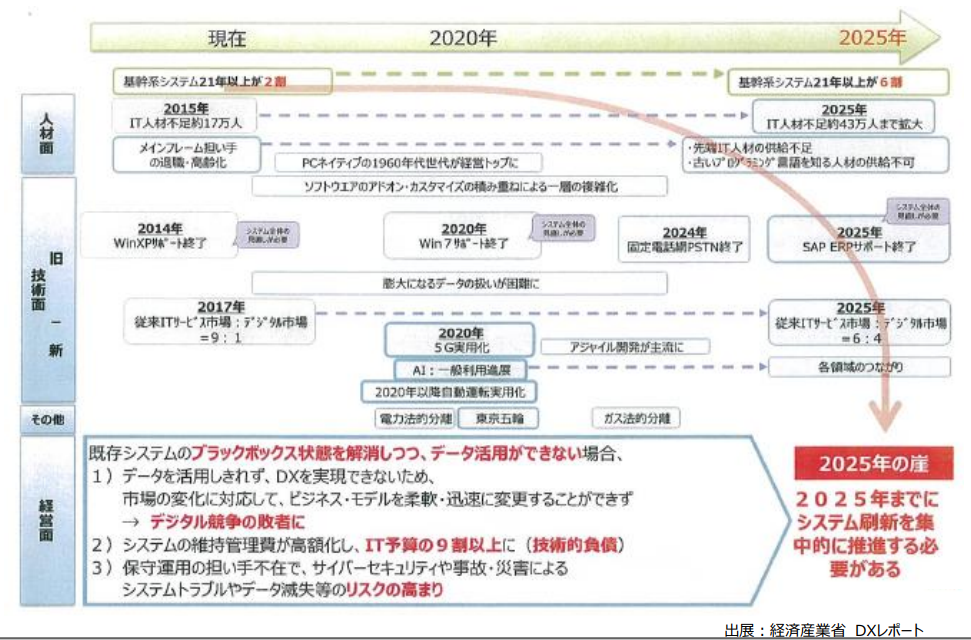
上記はあくまでも想定上のシナリオです。 ですが、デジタル化の波に乗り遅れ、いざ切り替えと思ったときには手遅れだった、などという事態は絶対に避けたい。このような未来を迎えることのないよう、皆さんと共に、未来を見据えた製造現場のデジタル化を進めていきたいと考えています。
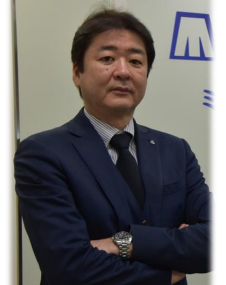
【講演者】
SIer協会 幹事(FA・ロボットシステムインテグレータ協会)兼
ミツイワ株式会社 スマートファクトリー推進部 部長
泉 貴史 氏
【略歴】
ロボットシステムの導入を通じて、経産省などとともに、ロボットシステムの導入の在り方についての協議に主要メンバーとして参画。IT企業としていち早く2012年から自動化(ロボット)ビジネス
事業を立ち上げ、Industry4.0、IoTを経て、スマートファクトリーへ大きく舵を切った。国の取り組みや中堅・中小製造業での事例を踏まえた講演、コンサルティングの支援実績を多数持つ。
「専門分野」
- ロボット導入・運営のコンサルティング支援 ‐IoT導入・運営のコンサルティング支援
- スマートファクトリー推進のコンサルティング支援、スマートファクトリー診断サービス
- 工場によるセキュリティマネジメント
- 既存情報システムと専門特化したFA・ロボットとの最適化支援